We got our temporary woodstove |
Electrician started |
Roof tiles and gutter finished
This week the roof tiles and gutter were finished. From here, our main outdoor task will be the outer wall, and indoors we will mount gypsum plates and isolate walls.
Monday 5 October
Today the building company came and mounted the gutters. Then they placed the last row of roof tiles. With that, I can reuse the planks on the scaffold we had lying at the top level for the roofers. When the gutters are finished, it becomes more urgent to lead the water from the gutters away from the building with downpipes. We will need to look into that. We have the downpipes lying in their original package, but they will need to be mounted on top of the red planks, and we first have work to do with that.
We continued our planning for the red planks this evening. There is simply no ready-made solution for us. Every expert in the field is doing the details differently, not entirely applicable to our situation. We are almost done with the window plan, though. This evening we studied how windowsills are made the Swedish way. Cut and folded a windowsill model from a paper after looking at instruction videos. There will be one upper windowsill on top of the window and one at the window’s bottom. I will figure out how to make these; it is impressive.
Then we revisited the nails problem. Manual nails are thicker to avoid that they will bend when operated with a hammer. Thicker nails more easily split the wood. Manual nails come in almost any length, but the thickness is always a direct function of the length, likewise, with the regular flat head’s size. One could select a bulb head, but we could not find those in stainless steel, so we got two expensive boxes of thick flatheads.
Tacker’s nails are thinner because they are shot into the wood with a tacker. I like that. They tend to stop at a maximum length of around 60 to 65 millimeters. I would like to have a smaller head on the outer planks, and I want to have thinner nails compared to the manual nails. I need to measure the width of the beam to make a correct decision. I will do that on Wednesday.
There is a complete tacker landscape out there. You start searching and get into brads—straight brads and angled brads and obviously of various sorts of steel and surface material. We are interested in the stainless nails to avoid rust issues, which is the most expensive sort. Galvanized nails are cheaper, but they will rust after a while.
The tacker brads usually have thinner nails. It is also possible to have the nails in brads bound by paper or metal wire, and then the nails can be thicker. With a longer distance between the nails in the brad, the heads can be more prominent, sometimes called D-heads. Nails in coils have an even longer distance, and the longer the distance between the nails in the coil or brad, the more the nail looks like a regular manual nail. With that, the nails can also get longer again. The nails can be smooth, but they can also have rings or a slight screwlike shape. That way, they have a better grip.
Then, of course, it is the tacker, how it is driven. Is it battery powered, pressured air for use with an air compressor, or is it with a gas and battery solution? The battery-powered tacker needs to have a massive battery. That is not so nice because of the weight. Until now, I thought we would get ourselves an air compressor and run a hose to the place we want to work at and use a lightweight tacker on compressed air. For that, we need a compressor. That is a machine we don’t have yet. I am sure that we will have a compressor one day, but I am not sure that it is currently the correct solution for our needs. I am not sure anymore. That compressor requires the generator to go continuously, and that is not nice. Yesterday I found the gas solution. Is it a CO2 gas it is using? It sounds like the gas is ignited, and the explosion is used to drive the nail into the wood.
I also wonder if various brads and coils are interchangeable between brands of tackers. I cannot risk having nails not fit for the tacker. I would hate that because we already got two packages of long and thick stainless steel nails that I will not use.
In October 2017, I started using Grammarly. Tonight they told me I had written over three million words. My current writing streak is 75 weeks in a row. Look, I am a native Swedish. This text that you are reading here is based on proper spelling. It is so much more fun to write for an audience and myself when I know that I am doing it to the best of the abilities of my spell-checking software and myself. I am also fond of the intellectual challenge of pleasing Grammarly, and sometimes they lose, and I win. But that is not often the case—preposition at the end that is a killer. I love Grammarly, but how do you operate the buttons with the keyboard? I got my hands on the keyboard, let me keep my hands on the keyboard.
Tuesday 6 October
This evening we did not go to the new house—the research for nails and tackers continued.
Wednesday 7 October
Today I worked in the morning. The afternoon was designated for going to the new house and continue work on the red planks. It had rained 27 millimeters since last time. We had one crucial thing to figure out: the exact width of the horizontal beams. They were between 24.2 and 25 millimeters, one inch. We thought they were 30 millimeters. We recalculated the necessary nails and found that before, we had aimed for slightly too long nails. We went to the city to get the new shorter nails. Suppose it was just one little forgotten box with nails so that we could continue, please. I silently hoped that capitalism would not fail me and provide the items I need and would like to pay. How hard can it be? These days more and more shops are getting more and more empty because why sell things people want when you can stack the shelves with the stuff they don’t want?
However, we found out that there was a misunderstanding about the shape of the nail’s head and what it is called. I had misunderstood it, my wife had it all figured out, but we had not talked about it. I thought that nails with a ball at the end were called ball heads. That was wrong; the ball-shaped are called lost heads in Dutch. Nails with a round head are called ball heads, but they do have a head, it is just rounded. Nails with a flat head are indeed called flatheads.
The shop did not have our nails, but the salesperson advised us to go to a second shop. The second shop was Isoro in the city. They gave away free masks at the entrance, and you could wash your hands with hand sanitizer. I was surprised because the shelves we full of stuff I do want to buy! We asked for the nails, and as so often, they also did not have precisely our nails. What they did have, though, was our nails in coils for a tacker.
Now, I had a chance to ask all the questions about this subject. To begin with, I wanted to know why our choice for nails was so uncommon. The salesperson had worked as a carpenter for over seven years and told us that we should have the ball-shaped stainless steel nails for our planks. He knew how deep the nails should be driven, not far at all. He said that professionals don’t need these as manual nails because they use tackers.
What he also could do was to put together a complete working package with all bits and pieces: the tacker for the nails we needed, an air compressor, a high-pressure hose, extension cord. We also got a piece to screw into the tacker.
Last but not least, we got the stainless steel nails with shiny round heads. The salesperson was also about to build a house in the area where we are building a house. He has a lot more knowledge about building than we do. Currently, he lived in a truck on his plot. We see that many young couples are creating a future in this area this way. They do it on their own with friends. He brought all our new equipment to our car and helped us load it into the trunk. He chuckled when he noticed the typical dirt road patina one our car.
I was delighted. Part of our struggle with the nails was due to a misunderstanding. When we returned to our new home, we unloaded all the equipment and connected it. I placed the coil in the holder.
The compressor was 1.1 kilowatt, and our old generator had not been able to run that compressor. How is it that things come together like this? The new generator hummed while the compressor buzzed. The tacker tacked. I tried a couple of nails, and the explosion in the cylinder is mighty. If you have your head above the tacker, then you get to enjoy the exhaust blowing out of the tacker.
Then we could start? No, we had to do a final calculation of the planks’ location, which did not amuse my wife. We had changed plans but not finished the calculations, so it was about time to do that. We sat down with Excel and recalculated the location of the planks below the window. The window sill is sticking out a little above the planks under the window in the new situation.
Now we could start? Well, I had to remove old planks first and free them from nails. When that was done, we could start sawing the left and right plank for the window. We decided that the left and right plank should be thinner at the window so that there is more overlap below the window for making that window sill a bit wider than the planks below the sill. There is a surprising amount of math going into the correct placing of the planks. You can see that the right plank has a cut out as long as the window on the photo. The bottom corner is thereby covering the corner below the window.
We were genuinely happy with the progress today, real progress without hassles—a few small glitches, such as turning the plank 180 degrees while sawing it. Usually no problem, but now the old nail holes came at the opposite side. We will fill these and paint over those holes. Another thing is that if there is a knot in the wood and the nail is not making it, it is essential to fix it before putting on the next layer for the rest very nice.
Thursday 8 October
It feels like it is raining without an end. That is not true. It is difficult to walk on the clay around our new house because it is very slippery when it is wet.
Ever since we ended our building holiday in the summer, we have been struggling using our spare time wisely. We are mostly useless to break up from work and get going to the new house and make efficient use of our evening. This Thursday, we ate leftovers from the day before, and before knowing it, we were at the new house and ready for action. Our neighbor had got his roof placed today. He got a gable roof, and I like that. Sorry to other neighbors with flat roofs, I don’t like flat roofs. It is just a style issue, I know, but I say it as it is.
We harvested three pumpkins. My wife planted the pumpkins on 11 June, and this worked out well. The tomatoes self-destructed in late august. We got very few of the tomatoes I planted. I think this was in combination with not giving enough water to the plants. It can also be that you have to plant tomatoes in a greenhouse? Some people say it is better to grow tomatoes in a greenhouse because they are less prone to get various deceases.
We plan to work on an indoor task during bad weather and an outdoor task with dry weather. Tonight we were going to work indoors for the first time according to this plan. We wanted to isolate the wall between bedrooms 2 and 3 on the first floor. It is not so that you can begin with a task and go ahead and do useful things. To begin with, you need to know what to do and why. We want to prepare walls for isolation because we need to free the space of the isolation material that we got stored. It will be easier for the electrician to work when that isolation material is eliminated.
With the “why” out of the way, it is time for the “how” to do the task. We need to place gypsum plates on one side of the inner walls, and with that, the wall is ready for being filled with isolation material. When isolation is done, it is time for the electrician to fill the wall with his pipes. When that is finished, the wall can be closed from the other side with a gypsum plate layer.
We will become aces in the plastering of gypsum plates!!! I have not done any plastering of gypsum plates, and I have no idea if it is a pleasant task, but I know we have very many square meters of gypsum that we will need to do, probably just a question of getting used to, I suppose?
The most significant challenge for gypsum is making all sides of the plate connect well with the next plate. A beam is required behind the plate, and we started talking about the benefits of stacking the plates vertically versus horizontally. Vertically would lend us fewer snippets of support beams, but our gypsum plate elevator would not be able to handle it. We got a lift for the gypsum plates, and the platform of the lift can be tilted, but it is not especially handy for vertical plates. Horizontal placement of the gypsum plates requires more snippets of horizontal support beams behind the plates. But we have no choice, really, because of our gypsum plate elevator. We ordered it last week, and the first parts arrived on Wednesday and the final part on Friday. We can put a plate on the lift and then elevate the platform to the ceiling. The gadget has wheels so you can roll it to the correct position as well. We got the extra tall version of this machine, and it requires the operator to be at least two meters tall typical Dutch people, and we don’t fulfill these requirements. I did not see that the package came with the operator included. I am still clueless about how this is supposed to work. For now, we use it in the standard configuration for normal humans.
We started to create support beams for the seams behind the plates after we decided to mount the plates horizontally. During our research for the pros and cons of orientation, it had become dark. Now we had to make a new decision: Are we going ahead turning on the light, or are we stopping for the evening and this was only half-past seven in the evening. We decided to turn on the light, meaning we had to turn on the generator and connect our lamp to the light. It was the first time we did this. When working like that, the generator is running continuously, and we sincerely hate that. On the other hand, the sooner we manage to prepare for electricity, the sooner our solar panels are activated.
We measured all the beams we needed and mounted a couple of them before we stopped working this evening. It felt great to work in the evening again.
Friday 9 October
Today we worked from home the entire day. I had time at the dentist to repair my tooth. In the evening, we had decided to go to the new house, lit a fire in our stove, and sleep in the new house. That was nice!
We went to bed and slept like royals in our new second-hand bed. I woke up once in the middle of the night, noticing that the sky was clear and you could see the stars. You could see the stars! I closed my eyes again and continued to sleep, happy that I could see the stars from our new house. I hope that light polluters will not spoil this effect.
Saturday 10 October
The next morning we woke up early and decided to “cease the day.” My wife washed our dish at our pump. We improved the sink, put an extra pallet on top so that the working height would be better. A beautiful peacock butterfly was hiding below the pallet.
The weather forecast told us it would start raining at 9 in the morning and continue for the rest of the day. That turned out to be an incorrect forecast. It was a beautiful day until around 3 in the afternoon, and then it started raining. We did not know that, so we decided to work indoors and continue on the tasks we started the day before.
The wall is made up of sections. I had decided that section number two will contain pipes for the ventilation of the rooms. There must be room for the pipes inside that wall. Because of that, I did not use regular beams but shallow multiplex ribbons. I used leftovers from our facia boards.
Just after the ribbons of the first two layers of gypsum plates were finished, our electrician came. He talked us through what the steps will be for his activities. He wants us to mark out the outlets, but that will be for another day.
We had finished the first two stripes of gypsum plates in the afternoon, an acceptable achievement.
At first, we wanted to stay at the new house in the evening, but we considered the things we had to do at our old home, recharging batteries, taking a shower, and eating. With all things considered, it was better to pack our things and go home.
We were satisfied with the work we did and with the meeting with the electrician.
During the work today, I took some lovely photos of birds.
Scaffolds are popular among birds. |
|
|
|
|
|
|
|
|
|
|
|
|
|
|
|
|
|
|
|
|
|
|
Sunday 11 October
We tried to get to the new house as early as possible. We decided to continue on the indoor tasks because the weather was not stable. Around noon we had finished the beams of the final stroke of gypsum plates. After that, we put up one full plate of gypsum before noon.
Today my brother in law came to us. The plan was to help us with the jack, lifting the container to be more level. His wife helped us secure isolation plates in the ceiling from falling.
We worked in the clay, and it rained. We got wet and muddy. It wasn’t enjoyable. The jack was okay; it is fine. There was no way to get the container lifted sufficiently because the jack sank into the clay. In the afternoon, we gave up on the exercise. When we gave up, the container was at the same height as before we started, but we had replaced the plates under the corners. I made no photos of this muddy event. So far, our 30-ton jack managed to avoid my camera!
When my brother in law had left, my wife and I continued with the gypsum plates. Not soon after, we had to turn on the generator so that we could have proper lights. The gypsum plate elevator is a tricky contraption. It is excellent, but the legs are sticking out, and usually, they are in the way.
Here ended the week.

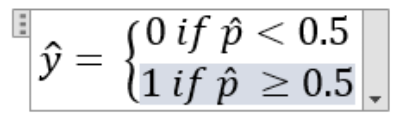
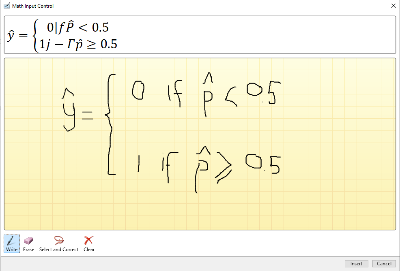
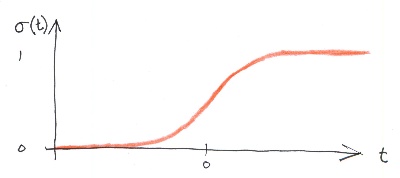
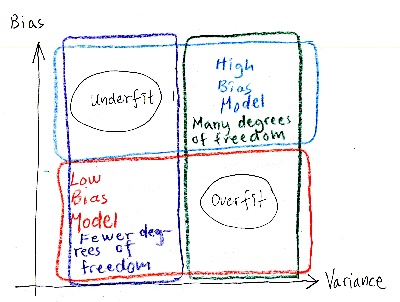
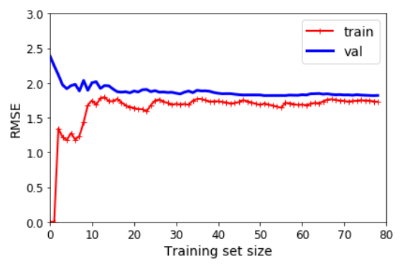
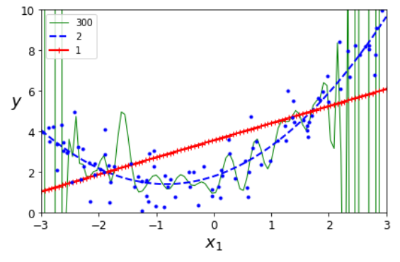



I moved from Sweden to The Netherlands in 1995.
Here on this site, you find my creations because that is what I do. I create.